The Artistry and Functionality of the Burl Bowl
In the timeless world of woodworking, where every grain tells a story and every craft bears the touch of the artisan, the burl bowl stands out as a captivating testament to nature’s imperfections and man’s creativity. This article delves into the allure of burl wood, exploring not just its aesthetic appeal but also the practical artistry involved in creating these unique, functional pieces.
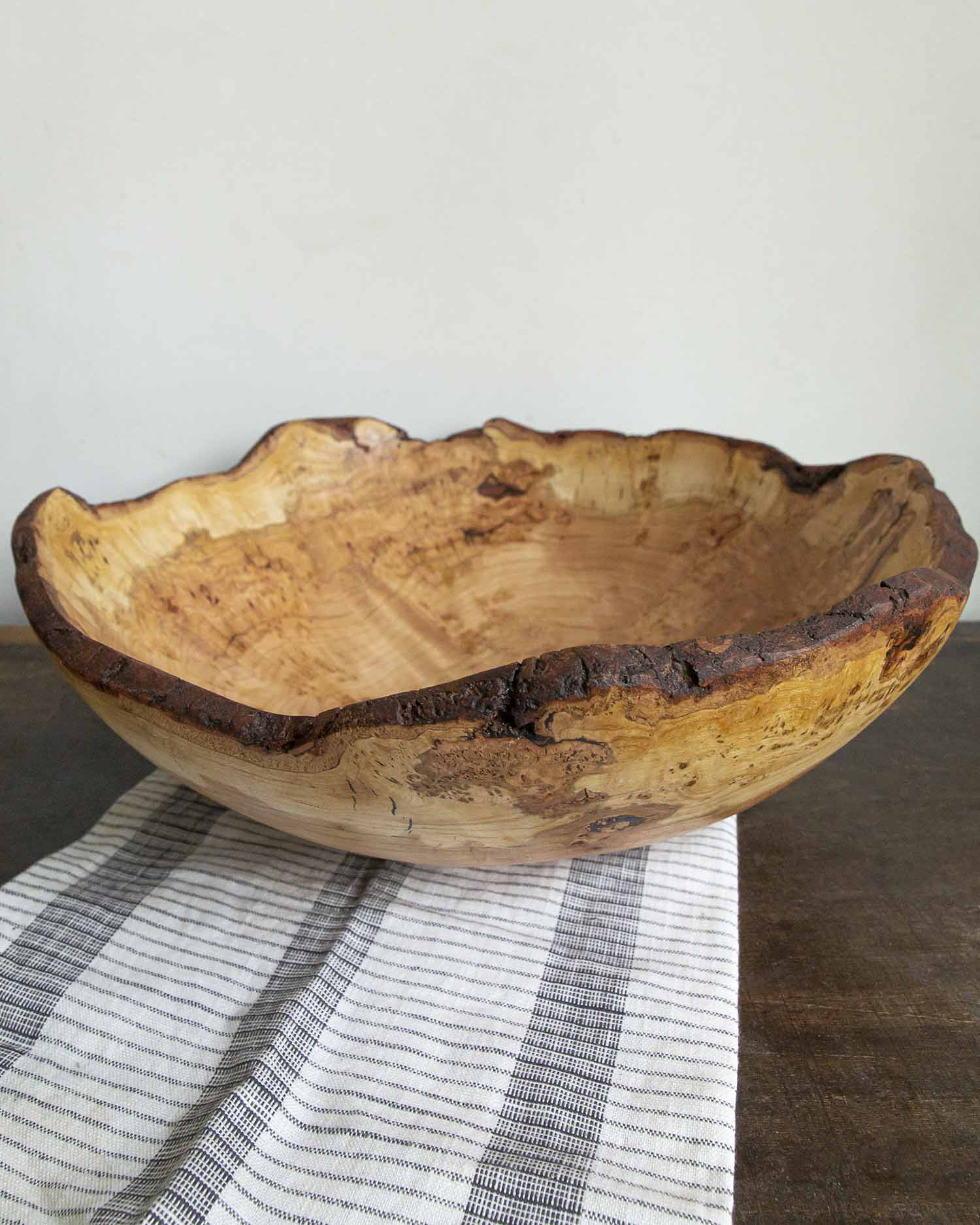
Burl wood comes from tree growths known as burls, which are essentially a tree’s response to stress, injury, or disease. These growths bulge out from the trunk or branches creating a mass of dense, often swirling, and aesthetically complex wood. Within this chaotic beauty, artisans find inspiration.
When you speak of burl bowls, one isn’t just referring to the shape of a container made from wood. It’s the celebration of an anomaly in nature. The burl, with its unpredictable forms, offers a canvas of intricate patterns in the wood’s grain, full of eyes, wild curls, and complex knots, each piece being as unique as a fingerprint.
The Making of a Burl Bowl
The process of making a burl bowl begins with the selection of the burl. Choosing the right burl is paramount. Woodworkers look for those with rich, live (spalted) edges or those that have an abundance of eyes—clustered knots that give a mesmerizing 3D effect when crafted into a bowl.
Once selected, the burl is carefully cut to reveal its hidden beauty. The initial rough shaping is about removing excess wood, getting to the core where the burl’s character is most pronounced. Lathes then come into play, where the burl is mounted, and the spinning motion removes layers to unveil the bowl’s form. This process demands a keen eye and steady hand, as errors could mar the natural beauty of the burl.
The turning process isn’t just about creating a bowl; it’s a dialogue between woodworker and wood. The turner must navigate the burl’s grain direction, which can be inconsistent, avoiding tears and ensuring a smooth finish. Burnishing, or sanding, follows, which brings out the chatoyancy—the cat’s-eye reflection of light often found in burl finishes.
After the initial turning, the burl bowl might undergo stabilization. This involves treating the wood with a resin that hardens it, preventing future movement or cracking. This step is crucial for functional pieces like bowls, where stability is key.
Decoration and Finishing
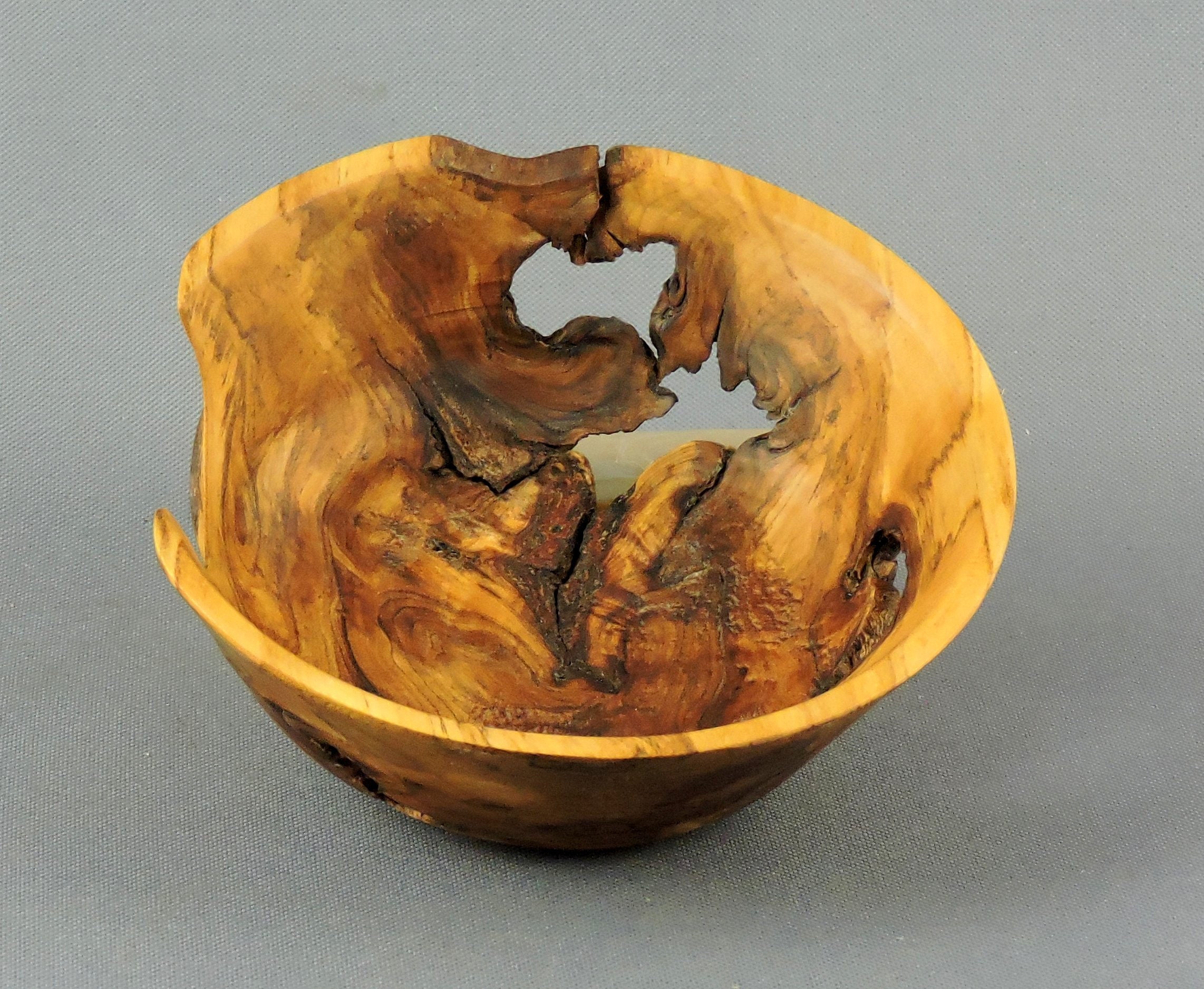
Burl bowls, despite their inherent beauty, often receive further enhancement. Some artisans engrave or stencil designs onto the rim, while others play with the contrasts of the burl’s natural colors. The finish applied is vital; it not only protects the wood but also accentuates the burl’s unique patterns. Lacquer, oil, or shellac can bring out depth and warmth in the wood, making the burl’s features dance in light.
Aesthetic and Functional Beauty
A burl bowl isn’t merely an object; it’s a piece of art for everyday use. From serving salads to holding fruit, these bowls elevate the ordinary. They are tactile pieces, where the hand feels the roughness of burl, the smoothness of the finish, and the symmetry of the turn.
Yet, there lies an irony in burl bowls: their beauty is such that owners might hesitate to use them, keeping them instead as showpieces. This hesitation highlights a curious interplay between function and aesthetic in woodworking. The burl, a flaw in the tree, becomes the essence of perfection in the hands of a craftsman.
Craftsmanship doesn’t end with the bowl’s creation. A burl bowl must be cared for. Oil treatments and protection from drying environments are necessary to maintain its lustre and utility. It’s living art, bound to the rhythms of nature and the care it receives.
To hold a burl bowl, then, is to connect with nature’s anomalies interpreted through human skill. Each burl bowl, whether on a dining table or displayed as art, speaks of a narrative of growth, imperfection, and the beauty in chaos. As you trace the contours of this work, each touch reaffirms the woodworking mantra: patience, precision, and reverence for the material.